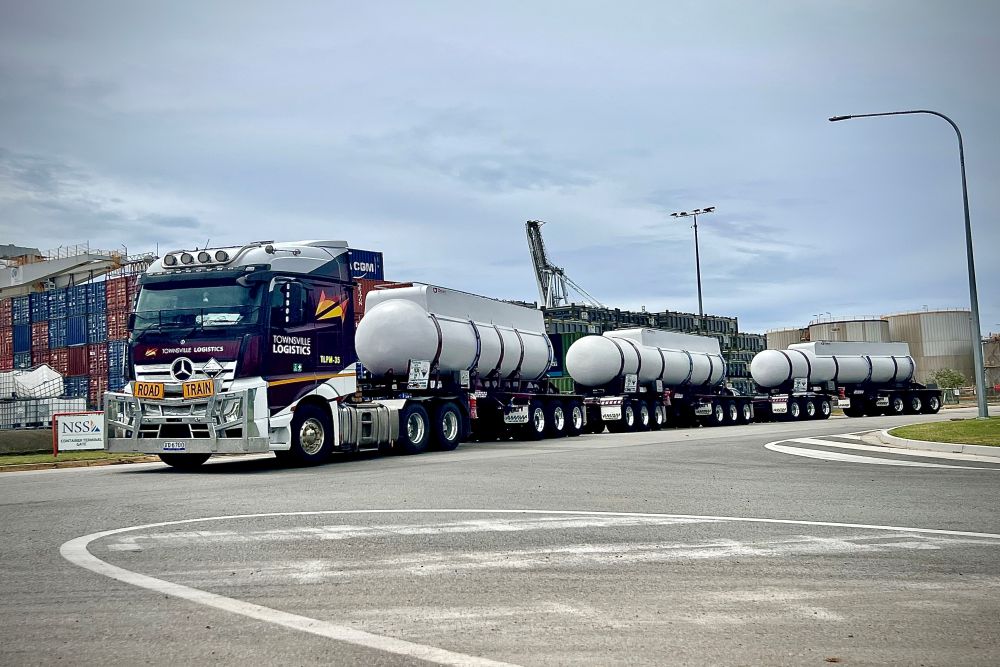
Australian Trailer Now Part of $1B Global Tank Business
Australian composite materials company Omni Tanker has launched a world-first composite triple road train that is able to move almost 100-tonnes of payload in a single haulage run while significantly reducing operational costs for its owner.
The triple road train, on the road for the first time in July this year with customer Townsville Logistics, has tanks made of advanced composite materials and built using engineering practices commonly found in aerospace.
Features include ‘mould-in baffles’ to restrict the movement of fluid in the road tankers. Preventing this surge enhances safety.
The collaborative project between Omni Tanker and Mick Murray Welding delivered a triple road train solution that has a 15 per cent gain in payload through its use of the advanced carbon fibre composite in its construction.
That allows for a reduction in the number of trips and associated emissions through the greater carrying capacity.
Omni Tanker CEO and founder Daniel Rodgers said: “Omni Tanker is combining advanced manufacturing technology with aerospace materials and heavy-duty trailers to deliver game-changing liquid payloads for the critical minerals processing industry – right here in Australia,
“Mick Murray Welding was crucial in achieving project success for our first product in the mining sector. They knew what the mining industry demanded, and they knew the harsh operating conditions they operate in, so it made absolute sense to combine Omni Tanker’s lightweight tanks with their high-tensile steel-skeletal trailers.
“Using advanced manufacturing techniques and outstanding partners, we were able to boost the payload carrying capacity of road tankers for chemical liquids from the current 85 tonnes per load, typical of stainless-steel tanks, to 98 tonnes – a fifteen per cent uplift.”
Three triple road train sets have now been delivered to Townsville Logistics for use in heavy acid transport across Northern Australia, with greater payload capacity meaning fewer trips, as well as associated cost and environmental benefits.
The global market for these liquid chemical tanks is valued at $800 million to $1 billion a year which is why the success of Omni Tanker’s tanker trailers is also being seen overseas.
All Chemical Transport in New Jersey, which has a fleet of 450 trailers, has 36 fibreglass reinforced plastic tankers and for more specialised work, uses carbon-fibre reinforced plastic tankers made by Omni Tanker.
The use of composites means there is no adverse reaction when carting corrosive chemicals so it guarantees the safe transportation of hazardous materials.
Omni Tanker’s cargo tanks being used for the North American chemical transport market are large-volume pressure tanks with a capacity of 5,500 US gallons (20,800 litres), a test pressure of 60 psi (4.1 bar) and a maximum allowable working pressure (MAWP) of 40 psi (2.75 bar). The Omni Cargo Tank is also certified in a range of different volumes and configurations.
These tanks are made by Omni Tanker and built on chassis made in the US. The Cargo Tank Motor Vehicle (CTMV) are approved for the transport of Class 5 and Class 8 chemicals throughout North America.
The Cargo Tank is made using Omni Tanker’s patented technology which covers the inside of the tank being a completely seamless thermoplastic corrosion barrier with no welds or joins (called OmniShield) and the outside of the tank being a high strength and lightweight carbon fibre reinforced polymer (CFRP) structure (OmniFort). The two layers are connected with Omni Tanker’s high strength interface technology called OmniBind.
Omni Tanker said that the seamless thermoplastic corrosion barrier provided a thick and durable interior to the tank that is highly resistant to damage or flaking to ensure high purity loads.
The carbon fibre composite structure provides the ultimate in lightweight and high strength to maximise payloads. The interface between these structures creates a tank with the greatest safety for high consequence liquids.
Omni A and AB tanks can be mounted to a rigid truck chassis or skeletal trailer in many different configurations based on customer requirements.
The largest combination of Omni Tankers used in Australia is a B-Double tanker, referred to as a B-Train in many countries, with a total volume of 40,000 litres across three tanks.
Omni Tanker started by making small tanks that were developed in Australia and sent to Europe. The program was then supported financially and logistically by the federal government through the Advanced Manufacturing Growth Centre (AMGC).
Found your perfect purchase? Let’s make financing just as easy!
Work with Australia’s best-reviewed finance broker for a great deal and a stress-free experience. With 2,500+ glowing Google reviews, you can trust you're in good hands! See what our happy customers say in Credit One reviews, or jump right in and crunch the numbers with our handy loan repayment calculator. Your ideal financing solution is just a few clicks away!